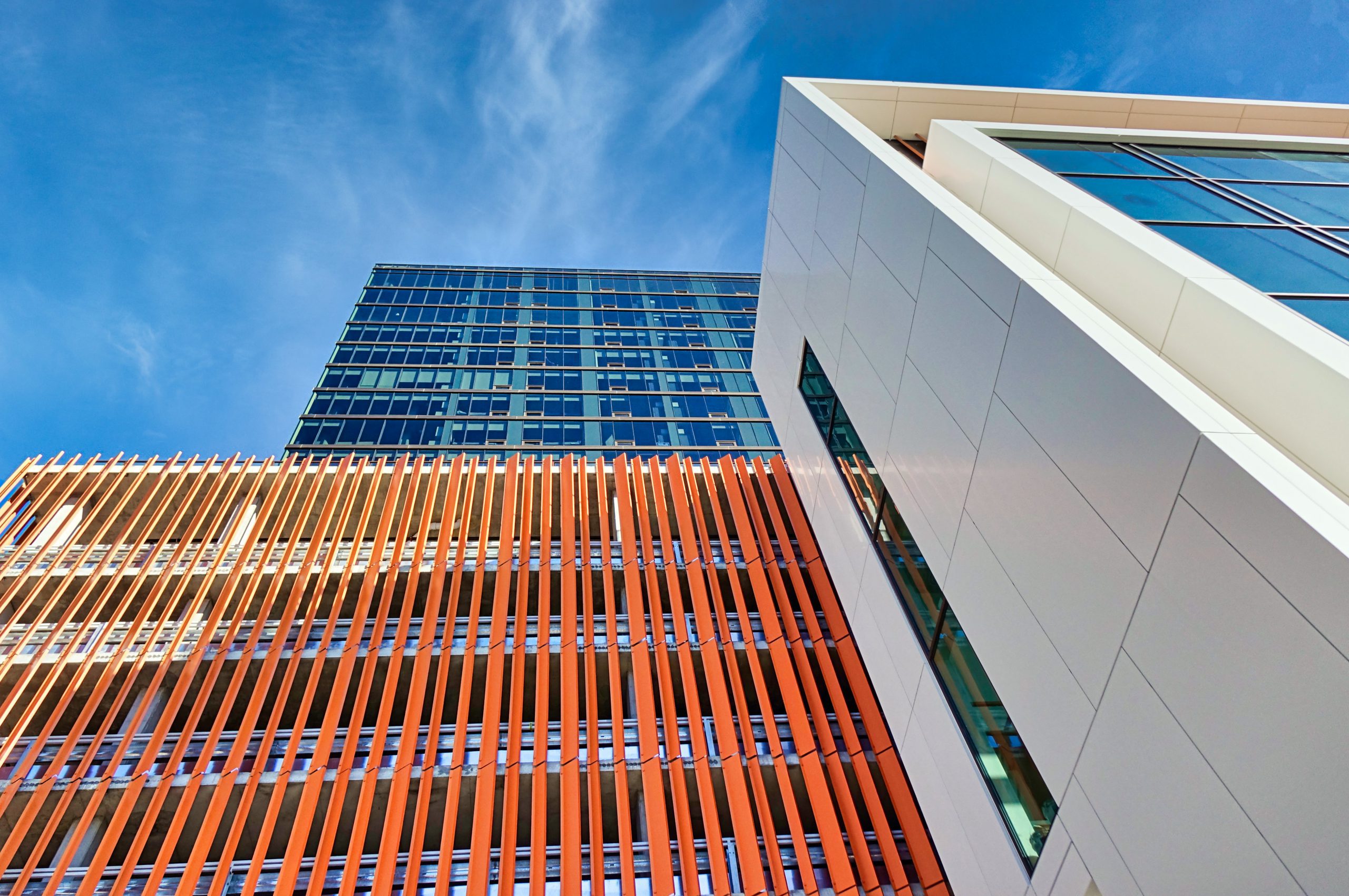
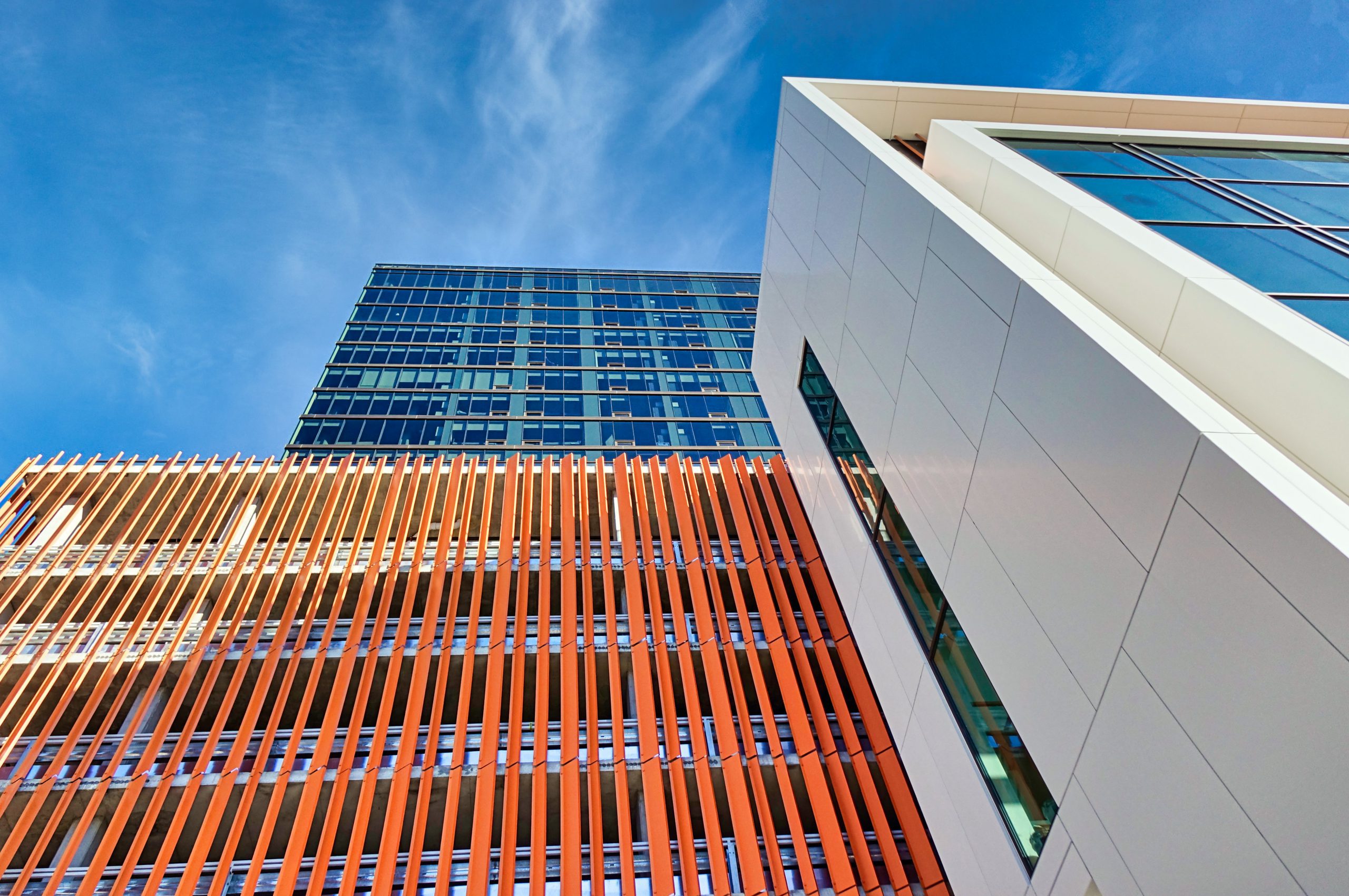
Finish is More than Color
For a look that lasts, don’t overlook these finish considerations.
Versatile metal composite materials (MCM) are a staple of modern architectural cladding known for bold appearances. According to Michael Bowie, technical support specialist at the ALPOLIC division of Mitsubishi Chemical America, “People like that MCMs can give their buildings a distinct, customized look. But you have more decisions to make than just what shade of red you want. When it comes to finish, it’s more than just color.”
The type of paint system and its application can significantly affect the appearance of painted metal panels and their longevity.
Selecting a Paint System
Two main categories of paint systems used in metal cladding are: polyester and fluoropolymer. Polyester paints are prevalent, inexpensive often have a wide color palette. They are often limited to internal use because of degradation when subjected to UV radiation.
The first generation of fluoropolymer paint system, PVDF, is widely used in the marketplace as a cost-effective solution. With a standard make up of 70% PVDF in a dispersion of 30% resin, the thermoplastic system is to remelting under high temperature and pressure and is more limited in its color range. “The resin component of PDVF has a milky appearance that can create muted colors,” explains Bowie. PVDF is also limited to a gloss range of 10-40. “Most building professionals know metal composite panels can give them the bright and shiny appearance that the design needs. But sometimes, that’s just not achievable with a PVDF.”
The second generation of fluoropolymer paint system, FEVE, is less common and costlier. But with a 100% FEVE clear resin, this thermoset solution can produce clear, bright colors in a gloss range of 10-70. “When you’re looking for bright and shiny, nothing does it better,” says Bowie.
Application Considerations
Spray coating, powder coating, reverse roller coating or direct die coating are application options. Bowie suggests that, when selecting products, considering these options may help minimize possible quality issues. “Is it bumpy? Is it uneven or thick? Does it have roping? How the paint is applied impacts the result and can contribute to the longevity of the finish itself.”
Spray coating and powder coating may lack the precision and uniformity needed for MCM cladding. For large, flat panels, coil coating, using reverse roller coating or direct die coatings are preferred. With reverse roller coating, paint is rolled onto a metering roller, which transfers paint to an application roller that applies the paint to the aluminum coil. This process controls paint thickness well and is readily available. However, the process requires a significant amount of paint in the coating pan and the finish is susceptible to a wake-like roping pattern.
Die coating extrudes paint through the mouth of a die and shears it off at the die, providing precise paint application, without roping. The system, while less prevalent, requires a higher-quality aluminum sheet to deliver a uniform, thinner paint application. With more control, die-coating uses less paint and supports sustainable manufacturing.
Good, Better, Best
Often a project specification has finish considerations to meet an AAMA standard. “Think of the AAMA specifications—2603, 2604, 2605—as good, better, best for architectural coatings. Many polyesters fall into 2603, some high-performance polyesters can meet 2604, but only fluoropolymers can meet the AAMA 2605 standard.” Bowie feels an AAMA 2605-compliant paint system is a smart investment.
This article was featured on Metal Architecture.